There are hundreds of different types of plastics available for injection molding. Each type has unique end-use properties and processing requirements.
Injection molding is a versatile process that produces high-quality plastic parts. It can be used to make a wide variety of products, including medical plastic components and automotive parts. Click the Plastic Injection Molding Companies In Florida to learn more.
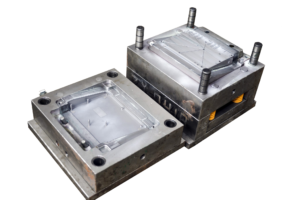
Injection molding can be a cost-effective option for manufacturers, product designers, and end users. However, the process is not without its challenges. It requires a significant investment in machinery, molds, and materials. It is important to understand how costs can fluctuate and plan accordingly. There are several factors that can impact the injection molding price, including the type of plastic used and the size of the part. Choosing a low-cost plastic, such as polypropylene, can help reduce production costs. The design of the part also plays a key role in its overall cost. Large undercuts, draft angles, and wall thickness can all drive up production costs.
In addition, a high number of defects can increase costs. Fortunately, these defects can be avoided by working with a manufacturing partner that has extensive experience. A skilled toolmaker can create a mold that produces fewer defective parts and saves you time and money. They can also recommend material options that are more cost-effective than the ones you currently use.
The injection molding process has a relatively low fixed start-up cost and the variable costs decrease at higher volume. Injection molding is known for its consistency and accuracy, making it an ideal choice for mass production. Moreover, it is highly efficient and has rapid cycle times. Multi-cavity molds can further improve the speed of production. Moreover, the injection molding process can handle a wide variety of thermoplastics.
One of the biggest factors affecting the injection molding cost is the initial investment in the mold. Injection molding is not an economical option for small batches of products, as the cost of creating a mold can be very expensive. Additionally, the tooling needs to be fabricated from steel or aluminum, which is an additional expense.
Lastly, the injection molding price can also be affected by the amount of raw material needed to complete a run. This can be caused by a number of factors, such as: wrong calculation of the material mixture; misuse of colorants; improper machine adjustment; and mishandling of the sprue.
Unlike 3D printing, where a new design can be uploaded and printed in minutes, the injection molding process takes much longer. Depending on the complexity of the product, it can take up to an hour for a cycle to be completed. This makes it important to consider the total time of the project when calculating costs.
Environmentally friendly
As the green movement becomes more prevalent in the world, many manufacturers are focusing on making their production processes as sustainable as possible. These changes can have a positive impact on the environment and also save money. These initiatives include using energy efficient equipment, reducing material waste, and selecting environmentally friendly plastics. Some manufacturers are even aiming for zero carbon emissions. These improvements can make your company more competitive and ensure that you comply with strict environmental laws.
When choosing a supplier for your injection molding needs, look for one that is committed to sustainability. Check their credibility by requesting testimonials from previous clients and seeing if they have any certifications. Also, inquire about the types of machinery they use. Electric machines are more efficient than hydraulic ones and reduce noise pollution. You should also consider whether they recycle their waste plastics and if they have in-house granulators.
Injection molding companies can also reduce their environmental footprint by implementing new recycling technologies and utilizing renewable energy sources. They can also optimize logistics and reduce the transportation distances of their raw materials to cut down on carbon emissions. Finally, they can participate in carbon offset programs to neutralize any remaining emissions.
Besides adopting energy-efficient practices, plastic injection molding companies are increasing their selection of eco-friendly materials. This includes biodegradable and compostable plastics, which decompose into organic compounds like water and biomass. They are a promising alternative to traditional plastics, which rely on fossil fuels and contribute to greenhouse gases.
A growing number of companies are choosing to power their factories with renewable energy sources. This helps to reduce their dependence on non-renewable resources and cuts down on waste. In addition, it improves their manufacturing process by reducing energy consumption and improving machinery efficiency.
Injection molding is a complex process that requires careful consideration when selecting the right polymer for a particular product. The main determining factors are the strength and functionality of the product, as well as the cost. Injection molding can be used to manufacture a wide range of products, including automotive components and medical devices. However, some plastics may not be suitable for injection molding because of their properties and composition.
Durable
Plastic injection molding is a reliable and cost-effective method for manufacturing products and parts. It’s a versatile process that can be used to make products of all shapes and sizes, including bottles, toys, and automobile components. It can also be used to create high-precision parts for complex applications and products.
The lifespan of a plastic injection mold depends on the type of material and the design of the part. Injection molds are expensive, so it’s important to understand how long they can last before needing repairs or replacements. This knowledge will help plastic manufacturers plan for maintenance and production capacity.
There are several factors that affect injection mold life expectancy, including the temperature of the melt, the operating conditions, and the environment. One of the most important factors is the injection mold’s class, which is determined by the Society of Plastics Industry (SPI) classification system. Injection molds are categorized into five classes, with class 101 being the highest level and corresponding to high-demand manufacturing environments.
Some plastics, such as acrylonitrile butadiene styrene (ABS), have high-impact strength and stiffness, making them suitable for high-performance applications. Others, such as polyethylene (PE) and polystyrene (PS), have lower impact strength but excellent tensile strength and rigidity. The material that you choose for your product will depend on your application, but you can mix materials to achieve the desired properties.
Plastic injection molding can produce parts that are more precise than CNC machining or 3D printing, but it’s difficult to change the design once the mold is made. Therefore, it’s best to use this technique for larger production runs.
Injection molding produces a finished product with a parting line, sprue, gate marks and ejector pin marks. These marks are unavoidable and may be visible on the molded plastic, although they shouldn’t have any cosmetic effect. Gate marks are the points where the melt-delivery channels (sprue and runner) join the part-forming cavity. Sprue marks are lines on the final plastic, typically along the parting line. Ejector pin marks are a result of minute misalignments, wear, gaseous vents and clearances for adjacent parts in relative motion.
Versatile
Plastic injection molding is a versatile manufacturing process that can produce complex and intricate designs in high volume. It uses a combination of injection and compression to form a wide range of products. It is ideal for producing durable, lightweight, and highly engineered components. It also has a low unit cost, making it an economical option for large-scale production. Injection molding is widely used in the automotive industry, for consumer electronics, and in the medical field.
Injection molding can create products with precise dimensions, which minimizes assembly and provides design flexibility. Its streamlined production process makes it easy to manufacture high-quality products. Moreover, it produces less waste than other types of fabrication processes, which reduces material costs and environmental impact.
A variety of plastics can be injected into the mold, including polycarbonate (PC), a tougher and more heat-resistant material that can withstand harsh environments and resist corrosion. Other commonly used materials include polyethylene (PE), LDPE, and PETE, which are resistant to moisture and chemicals. These materials are inexpensive and can be transparent, which is great for living hinge designs.
The tooling mold is the most important part of the injection molding process, and it requires a skilled team of professional machinists to make. Based on the design of the product, they create a blueprint and then assemble it into a functioning injection mold with sprues, gates, and an ejector system. It takes about 20 weeks to build a new injection mold, which is a significant investment.
Another key advantage of plastic injection molding is its ability to produce parts with fine details, including undercuts and overhangs. This allows manufacturers to experiment with intricate designs and internal channels, thereby expanding the boundaries of what is possible in product development. In addition, it enables the use of multiple components in a single part, which increases the functionality and durability of products.
The injection molding process is extremely efficient, requiring minimal post-processing and reducing the cost of the finished product. It also offers minimal waste, enabling producers to reuse scrap material for future injection molding cycles.